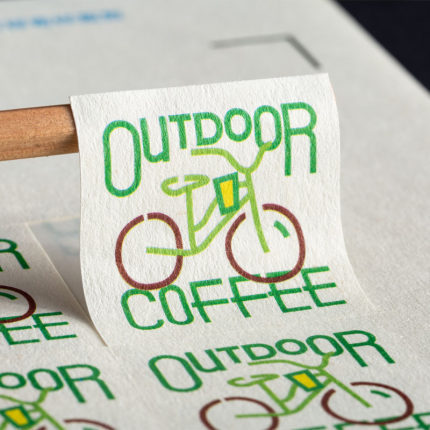
After the quantity of the cut-out adhesive material is confirmed to be correct, the name, quantity, size, and material lot number of the cut-off product shall be marked with a coated paper strip and attached to the positioning material of the entire batch of material.
The plate-making staff is responsible for signing the negatives and color samples provided by the design department, and checking the quality of the negatives, including the number of negatives, the identification content of the negatives, the degree of veracity of the edges of letters, lines, and dots, the dot density, and the degree of registration between dichroic slices. Etc. If the film is in error, a return form or rework slip should be completed and returned to the design department together with the film. For qualified film, the plate-making staff and designers sign and hand over the film receipt form; the inspection-qualified film should be kept clean and classified, and be stored in a special film bag. The mark should be made on the cover of the bag, including the product name and the quantity of the film. , package date, loan and return records, etc.
The plate-making staff selects suitable mesh and size screens and mesh frames according to the degree of fineness of products, and the tension is generally controlled at 6 to 8 kg/cm2 for at least 12 hours before removing the screen plate from the stretcher, and then Label the time and tension values on the edge of the screen. Before printing, seal it with a sealing tape and place it for 3 to 4 days (at least 24 hours). Before the squeegee, the new screen plate is degreased and roughened, and then the photosensitizer is poured into a glass in a dark room according to the preparation instructions of the sensitized plastic, and water is added to 80 to 100 mL, and the mixture is fully stirred until the photosensitizer is completely dissolved. Filter through a 200-mesh wire mesh, pour into the latex, mix thoroughly with bamboo chopsticks, cover and place in a cool place until the bubbles disappear. Squeegee when the general product selection 3 times scraping plastic, fine lines and dot product selection 2 times scraping gum. After the squeegee is laid flat in the oven, it shall not exceed 40°C for 0.5h until it is thoroughly dried.
Before printing, use cotton balls and alcohol to wipe the positive and negative sides of the film to repair the light transmission points. The printing plate should be clean and free of dirt. The selection of the screen requires that the pattern be no smaller than 15cm from the border. Under safe lighting, adjust the angle of most lines and the screen on the negative. The negative film should be adjusted to a reasonable angle without any moire. After the vacuum is drawn, the exposure time is selected according to different graphic content and different light sources.
After the exposure is over, the screen plate is immersed in the developing tank, and the screen plate is repeatedly shaken several times until the pattern is clearly visible, and then uniformly washed with a high-pressure water gun. At this time, the quality of the screening screen should be checked, and the self-inspection work should be done. The pattern edge is required. No jaggies, clear and transparent, no incomplete, no moire on screen, small dots are not lost, and large dots are not pasted. Absorb the moisture on the front and back of the screen with absorbent cotton, place it flat in the oven, and dry thoroughly below 40°C. After repairing the leaked version, the quality of the self-checked screen is correct, and a label is attached to the edge of the frame to indicate the product name, color type, color sequence, and copying time. The classification is matched and stored in the finished screen storage area. Related information is recorded on the screen table. The account includes all the contents of the area code, layer number, and the above-mentioned tags stored. Desk Book Arrangement Principle: According to the name of the customer, all products of each customer are arranged according to the figure number size.
Each batch of supporting screens must ensure the same tension and the same specifications.
In accordance with the requirements of the product process standards, the ink-transferring personnel shall provide long-term supply products according to the process card, and the new product shall receive the ink with corresponding performance according to the requirements of the drawings. When picking up, please check the following: whether the inks of the same model and different batch numbers are the same color; whether the inks of the same model and different batch numbers have the same consistency. After confirmation, fill out the warehouse receipt and use it.
When ink is dispensed, the main color ink and the auxiliary color ink are first judged, and they are roughly proportioned. Note that the auxiliary color must be added to the main color to record the ratio. After fully stirring, use the same screen as the official printing screen. The hardness of the scraped squeegee sample, after rapid drying compared with the standard color sample, and adjusted until the color is consistent; after the quality assurance personnel signed and confirmed, in the ink color record book to do a detailed proportion of various ink records, Paste the confirmed color sample.
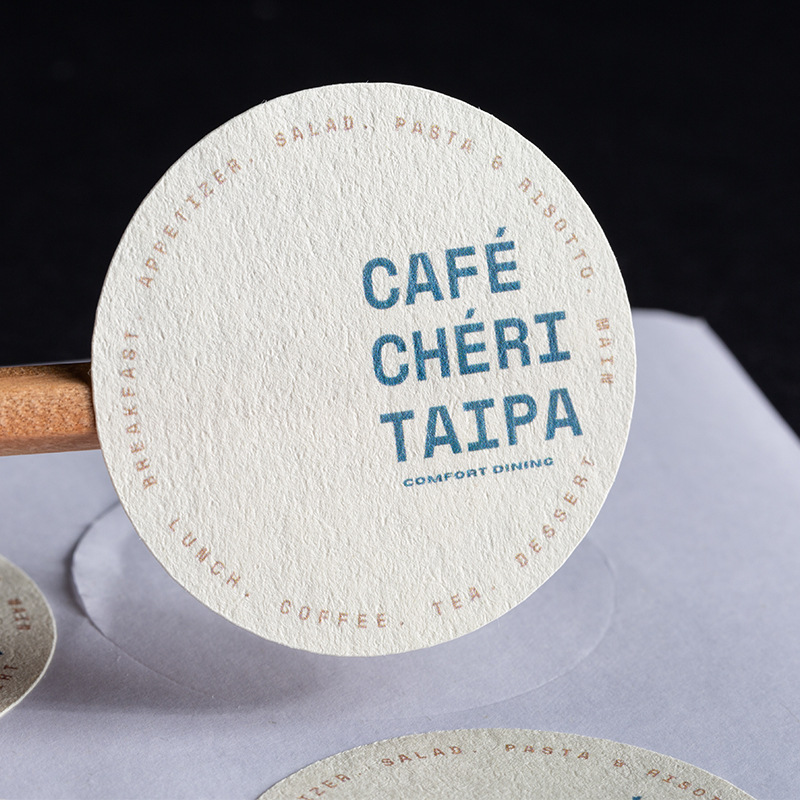
When the printing staff receives the ink, the ink is transferred from the ink-transferring personnel according to the amount of the material to be dispensed, and the appropriate amount of ink is provided for the graphic area. The thinner is uniformly added, and the proportion is 10% to 15%. The amount of ink issued by each printing machine is recorded; the printing is completed. Returned to the ink room, the ink transfer personnel responsible for the recovery of the remaining ink, and make records in the ink use registration form, the ink tank outside the logo.